Projet de 1ère année 2022 à Grenoble INP - ENSE3
Étudiants : Pablo Delgado, Maël Rouillon, Clément Beges et Mathieu Hartenstein
Encadrant : Nicolas Balcet
Structure de travail et outils : Fablab de GreEn-Er
Durée : 60h
Objectif : Dimensionner, modéliser et concevoir le modèle réduit d’une turbine Banki afin d’illustrer son fonctionnement et les différentes conversions d’énergie d’une centrale hydraulique.
Contraintes :
- Le démonstrateur se doit d’être facilement transportable
- L’écoulement de l’eau dans la turbine doit être visuel
- Essayer d’utiliser au maximum des matériaux de récupération
Pourquoi ce projet ?
Afin de diffuser au mieux la technologie libre de turbine Banki d’Hydr’Open, l’association se doit d’avoir du matériel pour se présenter. Le démonstrateur servira donc dans des événements tels que des forums d’associations, des rencontres liées à l’hydraulique ou encore pour sensibiliser les élèves aux enjeux de l’hydroélectricité. Finalement, le démonstrateur servira aussi d’exemple concret de projet de 1ère année pour les étudiants intéressés par Hydr’Open.
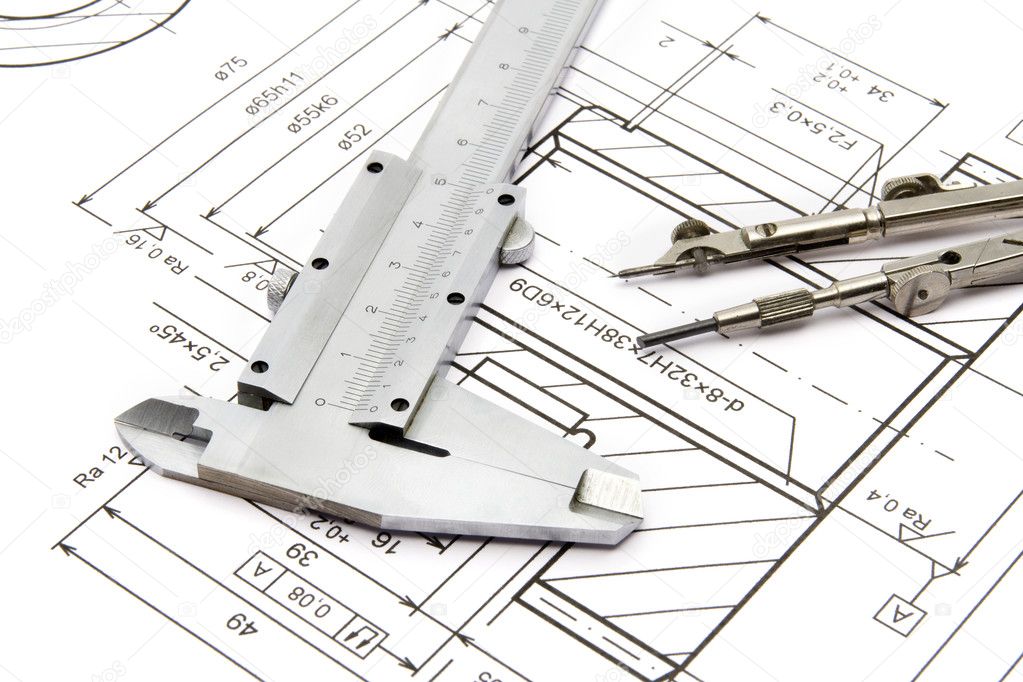
Dimensionnement
Le choix du montage
Le but du démonstrateur est d’avoir un aperçu du fonctionnement d’une turbine hydroélectrique. Recréer un montage avec un réservoir en hauteur permettrait de représenter au mieux le fonctionnement réel et connaître précisément la charge avec le point de fonctionnement, mais le montage risque d’être compliqué à réaliser et à transporter.
Nous avons donc choisi de réaliser un montage horizontal sans hauteur de chute directement relié à la pompe réglable permettrait d’avoir une charge réglable et donc des dimensions plus souples. L’énergie mécanique récupérée par la roue permettra, après avoir été transformée en énergie électrique, d’allumer une LED disposée sur le côté, comme sur les schémas ci-dessous.
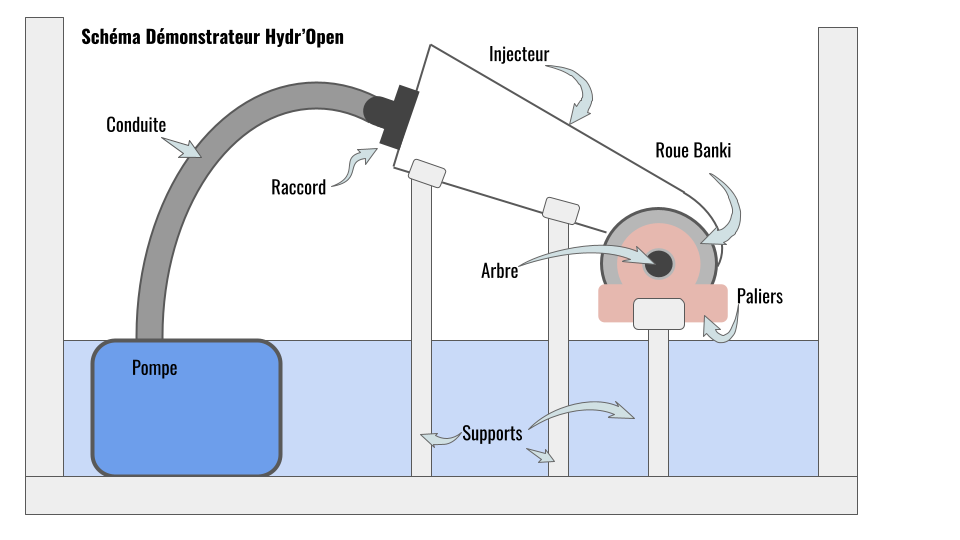
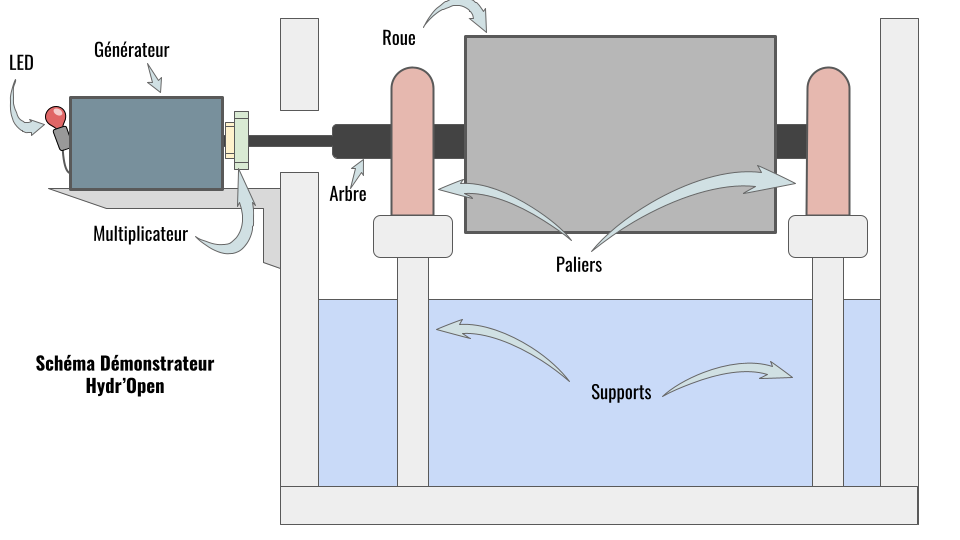
La pompe
La pompe choisie doit avoir un débit suffisant pour pouvoir faire tourner la roue, tout en étant submersible, compacte et compatible avec notre budget. Nous choisirons une pompe à débit réglable de sorte à atteindre la vitesse de rotation optimale de notre turbine. On optera donc pour une pompe de 5200 l/h à débit variable. La pompe est fournie avec 4 raccords de diamètres différents, permettant d’avoir plus de libertés sur le dimensionnement de la conduite.
- Pompe à débit variable
- Raccords
Figure 2 : Pompe à débit variable (à gauche) et ses différents raccords (à droite)
Le générateur
L’énergie mécanique récupérée par la turbine doit être transformée en énergie électrique grâce au générateur. Chaque générateur a une vitesse de rotation nominale différente, tandis que la turbine tourne à une vitesse de rotation fixée par le débit injecté ainsi que par ses dimensions. Il faut donc modifier la vitesse de rotation en sortie de la turbine pour qu’elle corresponde à la vitesse de rotation du générateur. On utilise alors un réducteur sous la forme de plusieurs étages d’engrenages. Le rapport de réduction sera déduit suite aux premières expérimentations sur la turbine car on ne connaît pas exactement la vitesse de rotation de notre turbine.
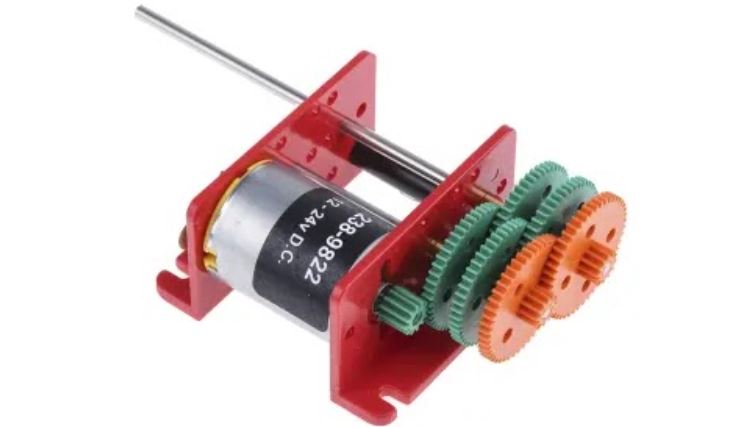
Pour avoir un large choix de vitesses, nous avons choisi d’acheter un motoréducteur avec plusieurs étages de multiplication pour pouvoir nous adapter au mieux.
Nous avons acheté un moteur 3V, 1,6W qui nous permet de nous adapter à une vitesse de la roue variant entre 1 et 2300 tr/min
adzdasazdFigure 3 : Motoréducteur
La roue et l’injecteur
Pour le dimensionnement de la roue en tant que telle, nous nous sommes basés sur des documents théoriques trouvés sur Internet, avec notamment « Banki-Michell Optimal Design ». Nous avons alors dimensionné la roue et l’injecteur en prenant un débit nominal de 3000 L/h. On obtient alors les paramètres suivants.
Figure 4 : Dimensions de la roue
Paramètre | Valeur | Description |
D1 (mm) | 80 | Diamètre extérieur de la roue |
D2 (mm) | 54 | Diamètre intérieur des pales |
Nb (-) | 30 | Nombre de pales |
λ (°) | 90 | Angle d’injection |
α (°) | 22 | Angle d’incidence de l’écoulement sur la roue |
β1 (°) | 39 | Angle entre la pale et le périmètre extérieur de l’injecteur |
β2 (°) | 90 | Angle entre la pale et le périmètre intérieur de l’injecteur |
ρb (mm) | 14 | Rayon des pales |
δ (°) | 61.5 | Angle des pales |
a (mm) | 20 | Hauteur de l’injecteur |
B (mm) | 47 | Largeur de l’injecteur |
W (mm) | 70 | Largeur de la roue |
Nous étions partis sur une roue de diamètre D = 80 mm à 30 pales car c’est ce qui était préconisé sur les documentations disponible sur la Banki. Cependant, nous nous sommes rendus compte que l’insertion des pales compte-tenu de nos dimensions était complexe et que les pales étaient très rapprochées. De plus, le dimensionnement de la turbine avec le tableur appartenant à l’association Hydr’Open nous conseillait de réduire à 20 le nombre de pales. Nous avons donc choisi une turbine à 20 pales.
Fin du dimensionnement
Une fois les principaux éléments fixés, nous avons pu dimensionner le reste du démonstrateur, c’est à dire l’arbre et ses paliers, la conduite, le bac et les supports.
Les caractéristiques de l’arbre et des paliers est donné par les dimensions des roulements utilisés. Nous avons choisi des à bille de skateboard de type ABEC 7. Nous avons ensuite choisi de réaliser la conduite grâce à un tube de PVC plastifié translucide d’un diamètre correspondant aux raccords de la pompe (32mm). Le bac se doit quand à lui de contenir un volume d’eau suffisant afin de ne pas dénoyer la pompe, tout en restant compact. Nous avons choisi de réaliser une boîte de 30cm de hauteur, pour une surface de 45x22cm. Pour finir, les supports, aux nombre de quatre, servent à soutenir les paliers et à soutenir l’injecteur. Les supports de paliers sont horizontaux et de même dimensions tandis que ceux de l’injecteur admettent une légère inclinaison de 22°.
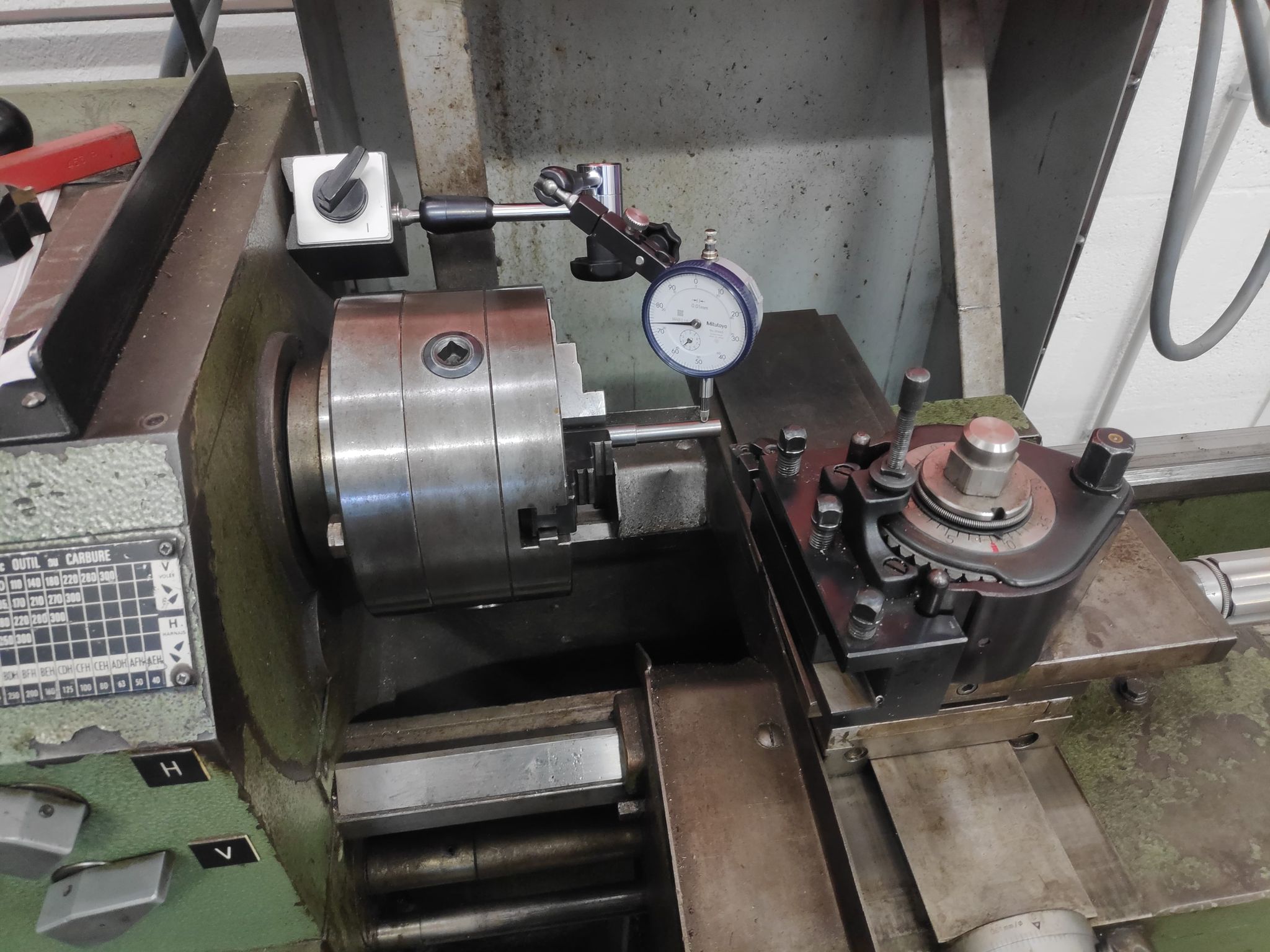
Réalisation et Montage
Réalisation de la roue
Figure 5 : Roue et ses flasques
La première étape a été la réalisation de la roue. Pour ce faire, nous avons dessiné les flasques latérales sur SolidWorks puis utilisé la découpeuse jet d’eau pour les réaliser à partir d’une tôle d’aluminium d’épaisseur e = 3 mm. Les rainures d’encastrement des pales mesuraient 14 mm avec un rayon de courbure de 61,5°.
Pour la fabrication des pales, nous avons découpé à la scie à métaux des petits cylindres de longueur L = 70 mm à partir d’un tube de PVC de diamètre D = 32 mm et d’épaisseur e = 2 mm. Puis nous avons scié chaque cylindre longitudinalement pour créer les pales avec une largeur l = 14 mm. Nous avons enfin poncé chaque pale pour les ajuster puis les avons encastrées dans les rainures au marteau. Finalement pour s’assurer du maintien en place des pales, nous avons chauffé les extrémités au décapeur thermique afin de les dilater fortement et ainsi les bloquer.
Réalisation de l’arbre et de ses paliers
L’arbre du démonstrateur a été réalisé en parallèle de la roue. Nous avons demandé aux usineurs de l’atelier de l’école de nous le fabriquer à partir d’un plan que nous leur avons fourni. La roue est montée glissante sur l’arbre. Elle est arrêtée en rotation à l’aide de 2 clavettes aux niveaux des flasques et en translation par des anneaux élastiques.
Le support de l’arbre est fait à l’aide de deux paliers avec roulement. Nous avons donc dû usiner l’arbre à nouveau aux extrémités pour pouvoir monter les roulements avec un ajustement serré.
- Pablo usinant l’arbre
- Tour
Figure 6 : Photographie de l’usinage de l’arbre
Nous avons finalement réalisé les paliers de support de l’arbre turbine à l’imprimante 3D destinés à accueillir les roulements et à être fixés sur notre support. Nous avons utilisé des roulements de roller ABEC 7 de diamètre extérieur D = 22mm.
- Plan SolidWorks d’un palier
- Roulement ABEC 7
Figure 7 : Plan SolidWorks d’un palier et roulement ABEC 7
Réalisation de l’injecteur et du raccord tuyau-injecteur
Nous avons décidé de réaliser l’injecteur en Plexiglass pour pouvoir voir l’écoulement au travers de celui-ci. Le plan de l’injecteur à été réalisé sur Solidworks puis découpé à la découpeuse laser.
L’injecteur est réalisé avec des côtés d’épaisseur différentes, les côtés latéraux de 10 mm et les supérieur / inférieur de 3mm. Nous avons usiné avec la CNC des rainures de 5 mm de profondeur dans les côtés latéraux afin de pouvoir encastrer les côtés supérieur et inférieur pour que l’injecteur soit solidaire.
Nous avons finalement plié l’extrémité du côté supérieur pour lui donner un rayon de courbure qui épouse celui de la roue et permet à l’eau de bien se répartir en sortie d’injecteur. Cette opération à été réalisée en chauffant le plexiglass à l’aide d’un décapeur thermique puis en pliant le côté à la main en s’aidant d’un guide qui avait le rayon souhaité.
- Découpeuse laser
- Côtés découpés
- Rainurage
- Injecteur afin pliage
Figure 8 : Étapes de réalisation de l’injecteur
Le raccord entre la sortie du tuyau et l’entrée de l’injecteur a été réalisé avec SolidWorks puis fabriqué à l’imprimante 3D. Le raccord à été percé et l’injecteur taraudé pour les visser et rendre les deux parties solidaires.
- Intérieur du raccord
- Raccord sur SolidWorks
- Injecteur monté et plié
- Raccord une fois imprimé en 3D
Figure 9 : Étapes de réalisation du raccord puis montage avec l’injecteur
Réalisation des derniers éléments du démonstrateur et montage
Nous avons maintenant réalisé les principaux éléments du démonstrateur, il ne nous reste plus qu’à nous occuper du bac, des supports ainsi que de la partie électrique.
Les plans du bac ont été réalisés à l’aide d’un logiciel en ligne ‘MakerCase’ qui permet de dessiner très facilement les parois d’une boîte en fonction des dimensions intérieures ou extérieures ainsi que l’épaisseur de la paroi. Le logiciel permet aussi d’ajouter des encoches pour permettre un assemblage plus simple.
Les supports en aluminium ont été réalisés avec la scie circulaire manuelle ainsi que la meuleuse. Pour assembler les différents éléments des supports, nous avons percé et taraudé les trous des cornières à la perceuse à colonne.
Pour réaliser la partie électrique nous devions tout d’abord connaître le rapport de réduction à appliquer au motoréducteur. Nous avons mesuré une vitesse de rotation à vide de 520 tours/min pour un débit de 4000 L/h. D’après la documentation technique du moteur nous avons alors décidé d’appliquer un rapport de multiplication de 16 pour sortir avec une vitesse de rotation adaptée à notre moteur et avoir une tension de sortie de 3V. Nous avons ensuite branché une simple LED en sortie du motoréducteur.
- Motoréducteur relié à la LED
- Bac une fois assemblée
- Supports
Figure 10 : Derniers éléments du démonstrateur
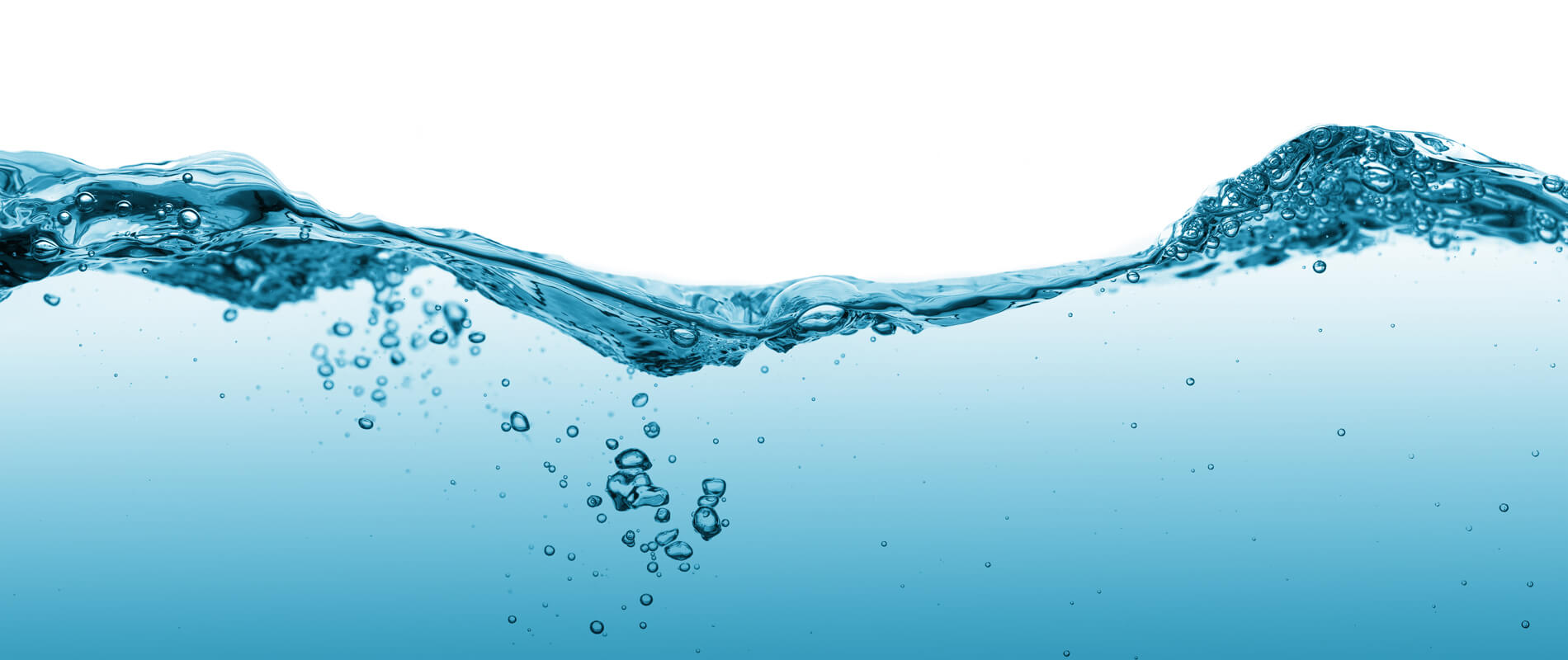
Résultats et Conclusion
Résultat :
- Démonstrateur fini
Conclusion :
Ce projet était très intéressant, il nous à permis de réaliser un dimensionnement de turbine, d’imaginer complètement un nouveau prototype mais aussi de le réaliser en partant de rien.
Dans un premier temps, le dimensionnement nous à conduit à utiliser les notions vues en première année dans les cours de mécanique des fluides en allant même plus loin en faisant des recherches sur des notions que nous n’avions pas encore abordées.
La deuxième phase était assez créatrice, nous avons dû imaginer à quoi allait ressembler la turbine, quelles seraient ses dimensions, en accord avec ce que nous avions calculé précédemment, pour cela le cours d’ouverture sur la conception mécanique à été très utile.
Finalement, la phase la plus longue à été celle de conception/fabrication. Grâce à l’accès aux différents FabLab et aux nombreux outils et machines outils disponibles nous avons été capable de réaliser une maquette “design” et fonctionnelle. Cette étape de fabrication nous a beaucoup appris sur l’utilisation des outils, les techniques et usages des ateliers et sur les possibilités diverses de fabrication.